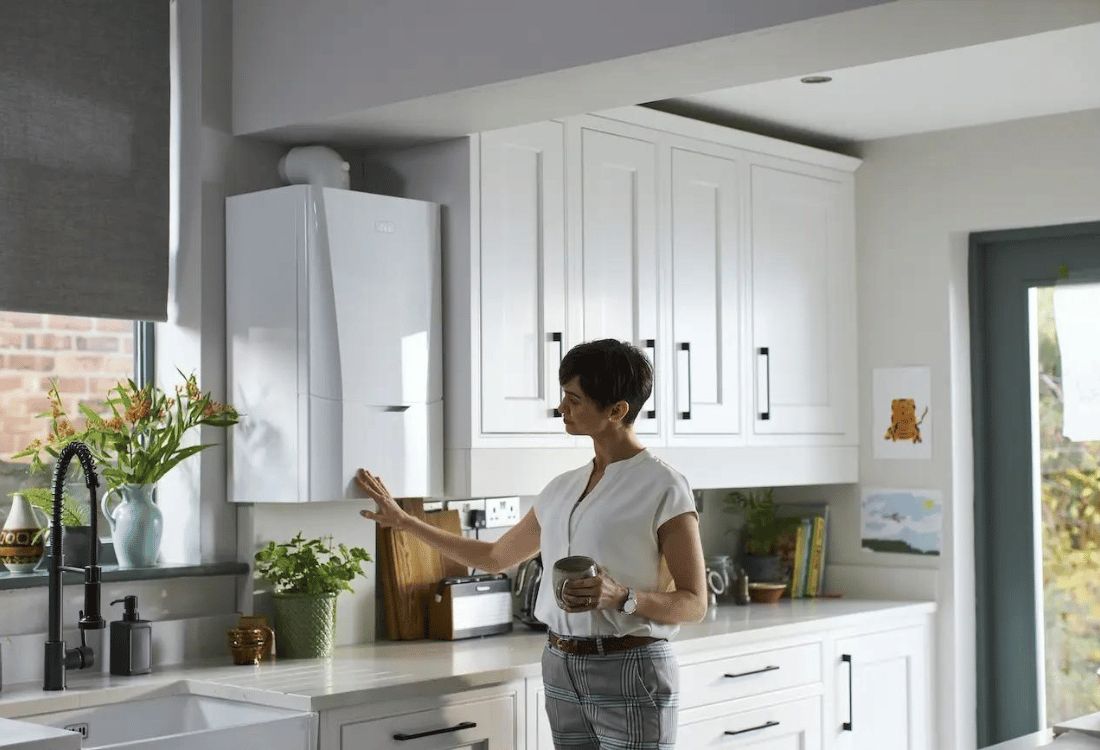
Decoding Ideal Boiler Issues: Troubleshooting Error Codes
With a trading history going back to 1906, Ideal Boilers are one of the leading lights in British boiler engineering, with a well-earned reputation for reliability, quality, and energy efficiency. Like any complex heating system, however, Ideal Boilers do occasionally manifest problems. These are expressed as error codes on the display panel, and are intended to help engineers quickly diagnose the fault and identify the correct replacement part.
As a homeowner, understanding the most common error codes can help you troubleshoot and resolve problems with your boiler more quickly, sometimes without needing to call an engineer. In this article, we’ll look at some of the most common Ideal Boiler error codes and their meanings.
FD: Low Water Pressure In The Central Heating System
Symptoms: Your boiler may not turn on or may shut off unexpectedly.
Solution: First, check the pressure gauge. The pressure should sit between 1.0 and 2.0 bar. If it’s below this range, re-pressurise the system by opening the filling loop valve underneath your boiler – making sure it’s closed once the correct pressure is reached! You should also inspect the boiler for any visible leaks. If this doesn’t work, you can try to bleed your radiators to remove any trapped air bubbles that might be causing low pressure.
Low water pressure can be a symptom of various issues, such as leaks in the heating system, a malfunctioning expansion vessel, or a failing pressure relief valve. If issues are persistently reoccurring then the best course of action would be hiring a professional heating engineer to inspect the system thoroughly, identify any leaks or malfunctioning components, and carry out the necessary repairs or replacements.
L1: Overheating
Symptoms: Common symptoms associated with this error include the boiler shutting down unexpectedly, unusual noises coming from the system, or noticeable fluctuations in water temperature.
Solution: To address an L1 error code on your Ideal boiler, you can start by attempting a simple reset following the manufacturer's instructions and check that the system pressure is within the recommended range. If the issue persists you’ll need to contact a qualified heating engineer to accurately identify and safely resolve any underlying issues, which can range from airlocks in the system, a malfunction pump or inadequate circulation.
L2: Flame Loss
Symptoms: An L2 boiler fault code indicates that the boiler might fail to ignite or keep shutting off.Solution: Ensure that your gas supply is consistent, and the gas metre has credit (if applicable). Check your gas company’s website to see if there are any known local problems and call them if in doubt. This can also occur if the gas flue is obstructed, frozen or blocked – a qualified engineer will be needed to resolve this problem.
L3: Ignition Fault
Symptoms: Boiler makes a clicking noise but doesn’t fire up.
Solution: This is a common issue in combi boilers that are continually switched on and off (e.g. for hot water while washing up). Inspect the ignition leads for damage or wear. This is generally a cheap and easy repair, but you’ll need an engineer to clean or replace them as necessary.
L5: False Flame Lockout
Symptoms: The boiler indicates flame detection when none is present.
Solution: This could be an electrical fault. Reset your boiler first, as this can often clear the issue, but if the issue persists, call an engineer. They will need to check the Air Pressure Switch and the Printed Circuit Board.
D And U: Diverter Valve Stuck In Mid Position
Symptoms: Your boiler has issues switching between heating and hot water mode.
Solution: Your diverter valve might be stuck, preventing it from moving freely. A stuck diverter valve can be caused by various factors, such as age, damage, or a build-up of debris. In some cases, the valve may simply need cleaning to remove any obstruction that is preventing it from moving freely. However, if the valve is damaged or has reached the end of its lifespan, it may need to be replaced.
In any event, due to the location of the diverter valve within the combi boiler your next step should be to seek the assistance of a qualified heating engineer. They have the necessary skills, knowledge, and tools to diagnose the issue accurately and determine the best course of action.
F And D: No Water Flow
Symptoms: The boiler will abruptly shut down and not switch on.
Solution: Check the boiler for closed water valves and verify that the system pressure is adequate. If this doesn’t work, call an engineer and request that they purge the air locks and ensure your pump is functioning correctly.
Next Steps
Having your boiler regularly serviced can prevent many of these issues from arising – we recommend an annual check by a Ideal qualified engineer. Always refer to your boiler’s manual for troubleshooting and safety instructions, but if you’re unsure about any issues or problems persist, the most effective way to prevent things getting worse is to speak to a professional heating engineer.
If you’d like to find out more or discuss a fault with your boiler, please contact Nicholson Heating today by calling 01670 331404.
Image Source: Ideal Heating